Laser welding is the preferred joining process in case of high requirements for seam quality and precise seam positioning. The laser beam is focused exactly on the component and is positioned with an accuracy of a few micrometers or better.
The precise alignment of the laser beam requires a pre-process and precise recording of the actual component position. By using a coaxial camera, ScaVis records the real position of the component from the viewpoint of the scan system. The setpoint setting of the welding seam to the correct position relative to the identified component features is achieved with the help of the comfortable software and the image processing.
Possible Applications
- Hairpins for the stator production
- Contact connections of power electronics copper elements
- Busbars of battery round cells
- Bipolar plates
- Heat exchangers and electrical components in white goods
ScaVis System Components
ScaVis can be combined with all Blackbird scan systems and it consists of components that were specifically optimized for the laser welding requirements:
- Expansion of the RSU User Software by an integrated ScaVis functionality
- High resolution camera for the coaxial attachment at the scanner
- Process specific lighting through a bar light or a ring light
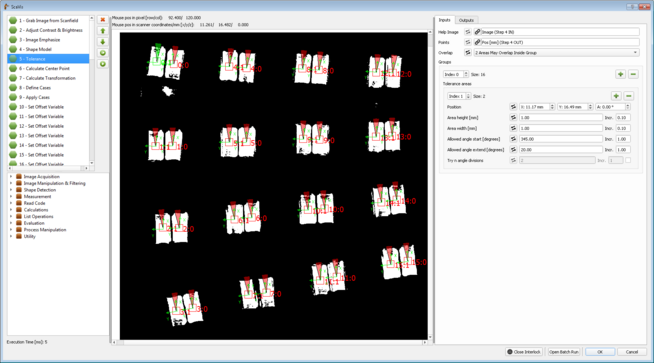
The ScaVis camera system is as flexible as the laser welding itself. The lighting elements are selected depending on the process and they can be flexibly actuated.
A variety of image processing algorithms permit a targeted and time-optimized highlighting of the relevant image features. The user individually parameterizes the subsequent data processing chain.
A Selection of Integrated Processing Steps:
- Convolution functions
- Edge extraction
- Straight and individual form identification
- Tolerance window
- Case differentiations
The worker interaction can be started automatically as soon as ScaVis identifies a component failure position. Based on the component photos, the users themselves decide whether the welding process must be aborted or whether the seam to be welded can be positioned manually.
ScaVis provides flexible extensibility and complete data transparency for the user. It can be used for different applications and it guarantees continuously high component quality even under challenging welding conditions and in a highly dynamic production environment.